If your boiler displays a fault code, it isn’t always something to worry about. It could be a simple fix that you can do yourself or it may require the knowledge of an expert.
The right solution for your boiler fault code
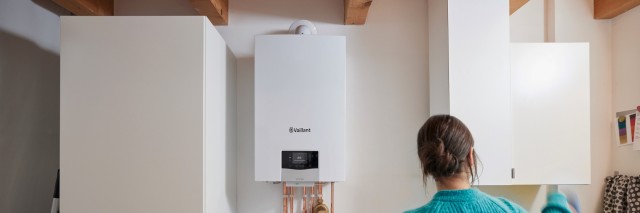
What’s the problem?
-
F13
The cylinder temperature sensor has short-circuited.
Possible cause:
- Fault in the electrical connection for the cylinder temperature sensor
- Cylinder temperature sensor defective
How to fix it:
- This is a case for an expert. Don’t try to solve it yourself as it can be dangerous.
- To solve it just call our customer service under 0344 736 0049 or find your nearest installer here. They can solve your issue quickly.
-
F20
The safety cut-out (SCO) interrupts the gas valve control. The gas valve was closed because the temperature of the flow or return temperature sensor has exceeded the maximum limit.
Possible cause:
- Insufficient/no water in the product.
- Fault in the electrical connection for the flow temperature sensor
- Fault in the electrical connection for the return temperature sensor
- Flow temperature sensor defective
- Return temperature sensor defective
- The pump is defective.
- 3-port diverter valve defective or blocked
- Water pressure sensor defective Volume flow sensor defective
- Black discharge via the ignition cable, ignition plug or ignition electrode
How to fix it:
- This is a case for an expert. Don’t try to solve it yourself as it can be dangerous.
- To solve it just call our customer service under 0344 736 0049 or find your nearest installer. They can solve your issue quickly.
-
F22
Low water pressure in the system
Possible cause:
- Insufficient/no water in the product.
- Fault in the electrical connection for the water pressure sensor
- Cable for the pump/for the water pressure sensor is loose/not connected/defective
- Water pressure sensor defective
- Pump operation interrupted
- Solenoid valve for the automatic filling device defectiveInternal expansion vessel defective
- Internal expansion vessel defective
How to fix it:
- This is a case for an expert. Don’t try to solve it yourself as it can be dangerous.
- To solve it just call our customer service under 0344 736 0049 or find your nearest installer. They can solve your issue quickly.
-
F23
The temperature spread between the flow/return is too great.
Possible cause:
- Air in the product
- Fault in the electrical connection for the flow temperature sensor
- Fault in the electrical connection for the return temperature sensor
- Flow temperature sensor defective
- Return temperature sensor defective
- Pump blocked
- Pump runs with insufficient output
- 3-port diverter valve defective or blocked
- Internal expansion vessel defective
How to fix it:
- This is a case for an expert. Don’t try to solve it yourself as it can be dangerous.
- To solve it just call our customer service under 0344 736 0049 or find your nearest installer here. They can solve your issue quickly.
-
F25
The flue gas temperature is too high.
Possible cause:
- Wiring harness defective
- If present: flue gas temperature monitor has triggered
How to fix it:
- This is a case for an expert. Don’t try to solve it yourself as it can be dangerous.
- To solve it just call our customer service under 0344 736 0049 or find your nearest installer. They can solve your issue quickly.
-
F27
A flame signal has been detected while the burner is off.
Possible cause:
- Gas solenoid valve not leaktight
- PCB defective
How to fix it:
- This is a case for an expert. Don’t try to solve it yourself as it can be dangerous.
- To solve it just call our customer service under 0344 736 0049 or find your nearest installer here. They can solve your issue quickly.
-
F28
The flame signal was not detected during the ignition phase.
Possible cause:
- Hard ignition takes place
- Gas isolator cock closed
- Gas connection pressure too low
- Air in the gas supply (e.g. during initial start-up)
- Incorrect gas type set
- Gas valve assembly offset incorrectly stored in D.052 and in. D.182
- Air intake pipe blocked
- Ignition failed
- Gas flow pressure too low
- Control electrode comes into contact with the burner
- Ignition electrode defective
- Burner defective
- Condensate pump (if fitted) defective
- Gas valve assembly defective/incorrect spare part gas valve assembly
- Interruption in the wiring harness
- Earthing defective
- Ionisation flow interrupted
- Fault in the flue gas route caused by recirculation or flue gas blockage
- Ignition transformer not connected
- Defective ignition transformer
- PCB defective
- Condensate in the combustion chamber due to a blocked condensate discharge
How to fix it:
- This is a case for an expert. Don’t try to solve it yourself as it can be dangerous.
- To solve it just call our customer service under 0344 736 0049 or find your nearest installer here. They can solve your issue quickly.
-
F29
The ignition following a flame loss during operation was unsuccessful.
Possible cause:
- The gas supply is interrupted
- Fault in the flue gas route caused by recirculation or flue gas blockage
- Earthing defective
- Air intake pipe blocked
- Ignition misfire
- Condensate pump (if fitted) defective
- Control electrode comes into contact with the burner
- Burner defective
- Interruption in the wiring harness
- Ignition electrode defective
- Gas valve assembly defective/incorrect spare part gas valve assembly
- Condensate in the combustion chamber due to a blocked condensate discharge
How to fix it:
- This is a case for an expert. Don’t try to solve it yourself as it can be dangerous.
- To solve it just call our customer service under 0344 736 0049 or find your nearest installer here. They can solve your issue quickly.
-
F61
The ASIC or µControl does not run in the defined times.
Possible cause:
- Fault in the electrical connection for the gas valve assembly
- PCB defective
How to fix it:
- This is a case for an expert. Don’t try to solve it yourself as it can be dangerous.
- To solve it just call our customer service under 0344 736 0049 or find your nearest installer here. They can solve your issue quickly.
-
F62
The flame switch-off was detected after a delay.
Possible cause:
- Gas valve defective
- PCB defective
- Ignition electrode defective
How to fix it:
- This is a case for an expert. Don’t try to solve it yourself as it can be dangerous.
- To solve it just call our customer service under 0344 736 0049 or find your nearest installer here. They can solve your issue quickly.
-
F75
The pressure change is too low when the heat pump is started up.
Possible cause:
- Water pressure sensor defective
- Internal heating pump defective
- System pressure too low Internal expansion vessel defective
- Insufficient/no water in the product.
- Air in the product
- Open circuit in wiring harness (LIN cable)
- Interruption in the wiring harness
How to fix it:
- This is a case for an expert. Don’t try to solve it yourself as it can be dangerous.
- To solve it just call our customer service under 0344 736 0049 or find your nearest installer here. They can solve your issue quickly.
HOW TO HANDLE COMMON FAULT CODES Play it safe: call an expert
We strongly advise that you do not touch your heating appliance yourself and always seek advice from an installer as soon as possible. They will have the expert knowledge to diagnose the issue and hopefully be able to clear the fault code. It’s important that if you smell gas, you need to vacate your property immediately and call the National Gas Emergency Service number on 0800 111 999.

Two ways for a quick solution.
NEARBY INSTALLERS
Installers from our Vaillant Advance loyalty scheme know your heating system from inside out. We help you find the best installer near you.
Find an installer
VAILLANT SPECIALISTS
Quick help: Our Vaillant expertise is just a phone call away. So, if you have any error codes, contact our customer service directly to arrange an appointment with one of our specially trained technicians. Profit from our know-how – since who knows it better than the brand who built it.
Get in contact
ENSURE OPTIMAL OPERATION WITH SERVICE CONTRACTS Fault code prevention: Safe comfort with our service contracts.
Even better than eliminating error messages? Avoiding errors. This is possible thanks to our 364 days live monitoring of connectivity ready heating appliances. It’s part of our service plan and, ensures optimum performance and safety. And if a fault does occur, you will receive the fastest possible appointment.
Advantages of service contracts at a glance.
Of course, you can simply book your service appointment when you need it. But a missed fault code can cause equipment breakdowns in the long run and result in unnecessary costs. With our Service plans, you can rely on our timely reminders.
-
Saving money
Regular checks and remote monitoring for efficient heating and energy reduction directly lower your energy costs. Also resulting in a longer lifespan of your boiler.
-
Individual comfort
The Vaillant service technician adjusts your heating system perfectly to your needs from remote and during every service. By that, you can always enjoy the ideal room and water temperature.
-
Safety first
We automatically remind you of upcoming heating maintenance to guarantee you the best care for your heating. And if the worst should happen and your heating system breaks down during the winter, you can rely on priority service and a technician who knows your heating for many years.
-
Unrivalled service and support
You can tailor your service package to your individual needs: You have the choice between cost-efficient basic contracts or comfort and all-in packages for no additional labour, travel and spare parts costs to control costs.
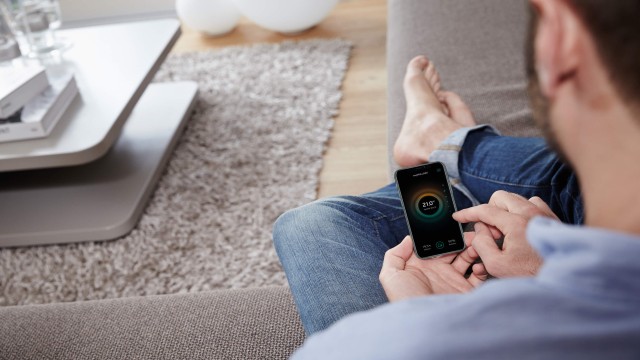
Smart comfort with our myVAILLANT app.
myVAILLANT offers a range of useful functions to control and monitor your heating system – conveniently via your smartphone. For example, you can detect faults in your heating system at an early stage and prevent them from occurring in the first place.
Advantages of myVAILLANT at a glance.
There are a number of benefits for using myVAILLANT, especially when it comes to boiler fault codes:
-
Effective & simple
Early error code recognition on your smartphone enables quick diagnosis and problem solving.
-
Safe & reliable
Detect potential problems early with the Health Check feature.
-
Proactive & cost-saving
Always keep an eye on your heating performance and optimise energy efficiency.
-
Smart & easy
Benefit from the user-friendly and intuitive app even without technical knowledge.
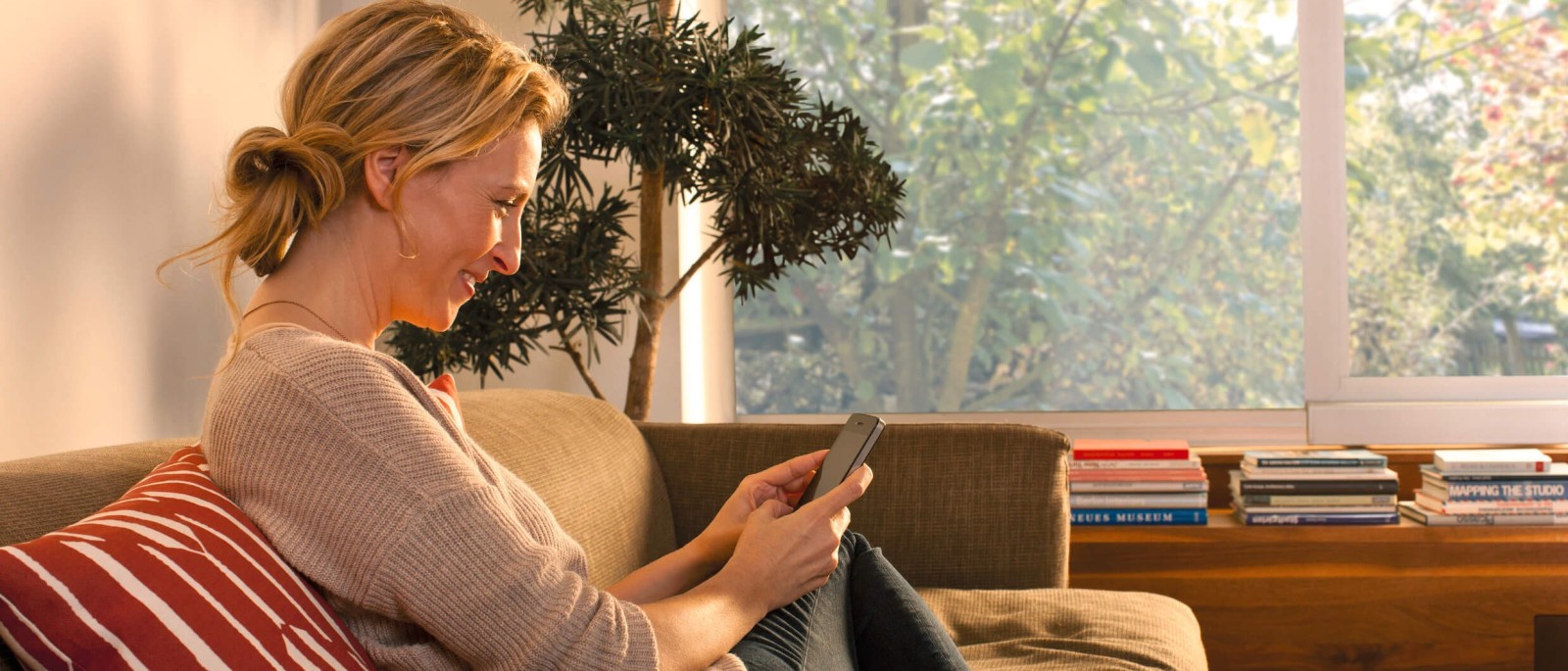
Manage your heating with myVAILLANT in three steps.
Contact your local installer to install a myVAILLANT connect pack**. **Only works with post 2006 eBUS equipped appliances. Please check the compatibility with your installer.
Have your myVAILLANT connect installed and connect your Vaillant heating system to your WiFi.
Download myVAILLANT app, register and activate your smart home subscription.
Contact your local installer to install a myVAILLANT connect pack**. **Only works with post 2006 eBUS equipped appliances. Please check the compatibility with your installer.
Have your myVAILLANT connect installed and connect your Vaillant heating system to your WiFi.
Download myVAILLANT app, register and activate your smart home subscription.
FAQs about boiler fault codes
-
Where do I find the Vaillant boiler fault code list?
The official boiler fault code list for Vaillant systems is only available from us. You find it at thetop of this page. We update it continuously so that it is always up to date. If you don't find your error code here, contact our customer service under 0344 736 0049.
-
How can Vaillant fault codes be prevented?
With our service contracts you can prevent many faults in your heating system. Because our experts keep an eye on your device, make sure the settings are correct and contact you proactively when maintenance is due. In this way, your heating system runs efficiently and safely in the long term. In addition, you can use the myVAILLANT app to conveniently view and optimise all the functions and data of your heating system on your smartphone at any time.
-
What is the Vaillant boiler fault F20 and how do you fix it?
The code F20 means: "The safety cut-out (SCO) interrupts the gas valve control. The gas valve was closed because the temperature of the flow or return temperature sensor has exceeded the maximum limit." To solve the issue please check our recommendation in the official overview list at the top of this page.
-
What is the Vaillant boiler fault F22 and how do you fix it?
The code F22 means: "No/insufficient water in the product or the water pressure is too low." To solve the issue please check our recommendation in the official overview list at the top of this page.
-
What is the Vaillant boiler fault F25 and how do you fix it?
The code F25 means: "The flue gas temperature is too high." To solve the issue please check our recommendation in the official overview list at the top of this page.
-
What is the Vaillant boiler fault F28 and how do you fix it?
The code F28 means: "The flame signal was not detected during the ignition phase." To solve the issue please check our recommendation in theofficial overview list at the top of this page.
-
What is the Vaillant boiler fault F29 and how do you fix it?
The code F29 means: "The ignition following a flame loss during operation was unsuccessful." To solve the issue please check our recommendation in the official overview list at the top of this page.
-
What is the Vaillant boiler fault F75 and how do you fix it?
The code F75 means: "The pressure change is too low when the heating pump is started up." To solve the issue please check our recommendation in the official overview list at the top of this page.